04 Mar 2021
Produttori diretti di automazioni per cancelli
Cosa significa essere produttori diretti diautomatismi per l’apertura automatica di cancelli?
Cosa rende questo aspetto un plus non trascurabile per l’installatore?
Facciamo una breve premessa: per l’installatore l’organizzazione della giornata lavorativa è un fattore fondamentale; la gestione del tempo costituisce, quindi, una delle risorse più importanti ed indispensabili della sua attività professionale.
Per ottimizzare il tempo a disposizione dell’installatore, è fondamentale che i sistemi di automazione per cancelli siano facili e intuitivi da installare e che siano affidabili: ovvero che non richiedano successivi interventi dopo l’installazione.
Se dovessimo riassumere questi concetti in due parole: facilità d’installazione e affidabilità.
Produzione interna e affidabilità del prodotto
La storia di Comunello inizia nel 1965 con la progettazione e la costruzione di stampi per automotive; un’attività che richiedeva grandissima precisione e conoscenza meccanica.
L’evoluzione dell’azienda negli anni, ci ha consentito di costruire un solido know-how nella meccanica di precisione; ovvero un insieme di competenze, conoscenze e abilità manuali e intellettuali.
Questo prezioso bagaglio, fatto non solo di conoscenza ma anche di struttura produttiva,lungimiranza negli investimenti e capitale umano, ci ha permesso di sviluppare la divisione Gate Automation che, partendo dalla progettazione, fino al prodotto finito, immette nel mercato una gamma completa di attuatori elettromeccanici per cancelli.
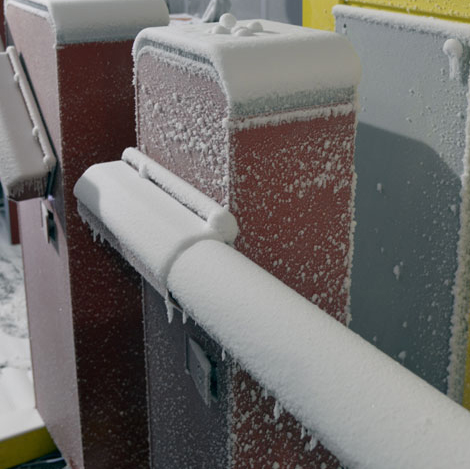
Avere il pieno controllo dei processi, ci permette di selezionare e controllare.
Selezionare e lavorare direttamente la materia prima, per noi significa mantenere un alto standard qualitativo fin dalla nascita del prodotto.
Controllare internamente tutte le fasi; dalla progettazione al collaudo finale ci permette di avere pieno controllo sul prodotto finito.
Test di sviluppo prodotto
Nella fase di ricerca e sviluppo di un prodotto, seguiamo un processo sequenziale di attivitàAPQP, di derivazione automotive, che ci permette di individuare dapprima gli standard tecnologici più adatti (materiali, soluzioni ecc.) e successivamente di monitorare e correggere con interventi rivolti ad ottenere un prodotto aderente alle specifiche.
Per questa fase progettuale così delicata, abbiamo predisposto una serie di test che coprono sia la parte meccanica che quella elettronica di prodotto.
I test cui vengono sottoposti i dispositivi, siano essi attuatori, centrali o accessori, riproducono cicli di vita del prodotto in tutte le condizioni prevedibili di stress:
- Test ciclici di vitain continuo di apertura e chiusura o di attivazione a carichi sovradimensionati per garantirne l’affidabilità. Nel caso specifico degli attuatori vengono impiegate strutture che possono essere caricate oltre il limite oppure nel caso delle barriere, dotando al massimo di equipaggiamenti per simulare il massimo stress.
- Test estremi di vita a cicli di funzionamento estremo quali continue inversioni per scorrevoli e barriere, funzionamenti in condizioni di disturbo generati dall’esterno nel caso di dispositivi elettronici e affini.
- Test in condizioni di temperature estreme che consistono in test ciclici di vita o di funzionalità sia alle bassissime temperature che alle alte temperature per verificare, discriminare e risolvere eventuali problematiche che si possono presentare in queste condizioni.
- Test debug volti a verificare l’assenza di comportamenti prevedibili non conformi alle aspettative. Questo significa che vengono testate le funzionalità di base generali e via via vengono poi verificate tutte le condizioni “particolari” meno frequenti nella vita del prodotto ma che possano ingenerare funzionamenti non previsti che possano mettere in difficoltà l’installatore o l’utilizzatore.
Per svolgere tutte queste attività, presso i nostri stabilimenti, disponiamo di aree specifiche con personale dedicato.
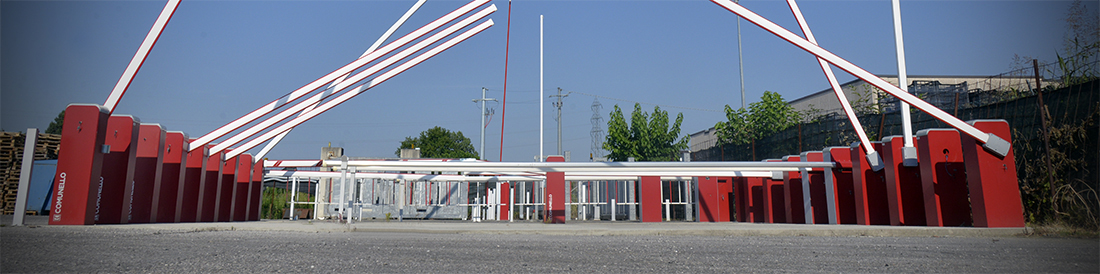
Controllo e test direttamente in produzione
Essere produttori diretti di prodotto, ci permette un pieno controllo durante la fase di produzione in serie.
Cosa significa nello specifico?
Il controllo attraverso un protocollo di test in produzione, permette di valutare la qualità di ogni singola componente, migliora la resa della linea di produzione e l’economicità delle risorse; garantendo conformità conle specifiche dell’R&D e le aspettative del mercato e riducendo drasticamente la possibilità di errore in fase di collaudo finale.
In questo contesto tutta l’elettronica viene collaudata al 100% prima di entrare nella linea di assemblaggio dove poi viene ricollaudata a fine linea.
Controllando la produzione possiamo intervenire prima che il problema si manifesti sul prodotto finito.
Test alla fine della linea di montaggio
Ogni singolo prodotto viene regolarmente testato alla fine della linea di montaggio.
La nostra produzione si avvale di linee di montaggio automatizzate e manuali composte da operatori specializzati, i quali alla fine del processo di assemblaggio, collaudano il prodotto attraverso un processo di accensione e misurazionedi parametri caratterizzanti la conformità dello stesso.
Questi possono essere la forza di azionamento, la velocità, il funzionamento dello sblocco e molti altri.
L’etichettatura finale del prodotto è garantita solamente dopo che il collaudo ha dato esito positivo, ne è quindi garanzia di tale processo.